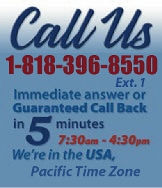 |
|
|
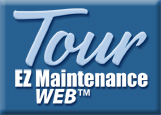 |
|
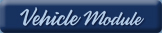 |
|
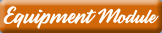
|
|
|
|
|
|
|
|
|
|
|
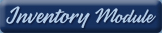 |
|
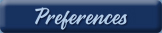 |
|
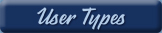 |
|
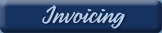 |
|
EZ Maintenance for Windows |
|
EZ Maintenance™ is also
available as a Windows's
program for the user seeking
a flat priced maintenance
software solution.
|
|
 |
Partial Client List |
|
EZ Maintenance™ for Windows
|
EZ Maintenance™ WEB |
|
|
|
Features |
|
- Schedule All Maintenance
- Equipment & Vehicles
- Full Inventory Control
- P.O.s, RFBs, Invoices
- Work Orders, Bar Coding
- Emergency Work Orders
- Email Alerts
- QuickBooks Link
- Send Work To Vendors
- Customer/Vendor Tracking
- Track Customers
- Maintenance Histories
- Access Passwords
- Supervisory Control
- And Much More!
|
|
Contact Information |
|
Pinacia Inc.
5699 Kanan Road, #349
Agoura Hills, CA USA 91301
Phone: (818) 396-8550
Sales Support: ext. 1
Tech Support: ext. 2
Fax: (818) 396-3524
info@pinacia.com
|
|
|
|
|
|
Next
Section:
Entering
and Viewing Equipment
|
Click here to see details
on Equipment Setup
/video/
|
Setting up
EZ Maintenance Web |
In
order for the Equipment Maintenance module to function,
basic information must be entered. The SETUP
menu is where entering basic data takes place. Once entered,
the information will never need to be entered again. This
one time entry makes data available throughout the application
to schedule preventive maintenance, create Work Orders, produce reports,
etc. You can either enter all data at one time or enter
the various data as you develop Work Orders and preventive maintenance
requirements. Entering all at once or as you go makes
no difference to the functionality of EZM Web.
|
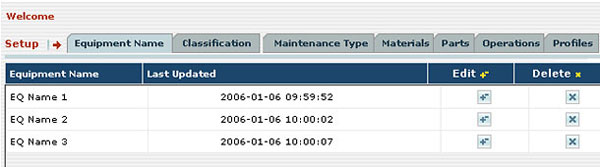 Enter data into the tabs of the
"SETUP" menu as follows:
Equipment Name: Allows you to define broad
categories of equipment.
Equipment Classifications: Allows you to
further classify equipment by physical location or other criteria.
Maintenance Types: Allows you to give names
to your different time intervals for performing preventive maintenance.
Materials: Here, you enter a comprehensive
list of the various materials actually used in maintaining your equipment.
Parts: This section is a list of individual
parts of equipment to be maintained so that you can schedule maintenance on
a transmission instead of a whole tractor, for example.
Operations: This is a complete list of the
individual steps required to perform your maintenance tasks.
Maintenance Profile: Building a profile is
what ties together all the other entries in the setup menu. Profiles are
essentially building your maintenance schedule. Your profiles will detail
what type of equipment is being worked on (Name), which group of equipment
it belongs to (Classification), how often it gets worked on (Maintenance
Types), what part of it is being worked on (Parts), what is necessary to
work on it (Materials), and how it is actually performed (Operations). By
creating a Maintenance Profile and then selecting that Profile from the drop
down list when entering new pieces of equipment, all preventive maintenance
events will automatically be set up and scheduled for that piece of
equipment from that date forward. Maintenance Profiles are an incredibly
powerful feature of EZM Web.
|
Some closing SETUP notes:
For maintenance management and quality-control purposes, data, (Equipment
Names, Classifications, Maintenance Types, Materials, Operations and so
forth), can only be entered from the main SETUP menu. To ensure consistency
throughout the program, the data cannot be entered 'on the fly' by
maintenance staff or workers handling the job or creating a Work Order. To
guarantee the information being used throughout the program is reliable,
data can only be entered in SETUP.
The Equipment Maintenance Module contains numerous reports
ranging from Work Orders to Maintenance Histories, etc.
These reports can be viewed or printed from the section
of the EZM Web tour that coincides with the particular
report purpose or from the main index of reports. The
Report Index is available for review by clicking
here. |
Next
Section:
Entering
and Viewing Equipment
|
|
|
|
|